Учёные, инженеры и сварщики предприятия – в основном, выходцы из «оборонки».
Высокая квалификация персонала и имеющееся оборудование позволяют ремонтировать сваркой или пайкой почти всё. Желательно лишь, чтобы это «всё» привезли к нам. Однако, для ремонта нетранспортабельных и стационарных объектов наши специалисты могут выезжать на место выполнения работы. Наиболее частый, типовой пример работы на выезде - ремонт смесительных и обогреваемых ёмкостей в пищевой промышленности.
Большинство работ по ремонту сваркой приходится на автомобили и строительную технику, а также мотоциклы. Основные из них – ремонт блоков цилиндров, картеров, выпускных коллекторов, топливных баков. Наряду с этими работами постоянно поступает в ремонт что-то нетиповое, например, коробчатая стрела подъёмника, ковш экскаватора, поворотная тумба экскаватора, цистерна большого молоковоза, и многое другое.
При необходимости, в технологическом процессе ремонта чередуют сварку с механической обработкой.
Узел или деталь, сдаваемые в ремонт, желательно (но не обязательно) помыть снаружи и, если внутри есть масло, слить его. Если восстанавливают элементы крепления (бобышки с резьбой, фланцы с отверстиями и т.п.), то желательно привезти ответную деталь, сопрягаемую с ремонтируемой: отверстия в ней используют как кондуктор, обеспечивая совпадение с резьбовыми и гладкими отверстиями в ремонтируемой детали.
Срок ремонта подавляющего большинства деталей и узлов – сутки-двое. Некоторые работы выполняют за считанные часы и даже минуты.
Срок гарантии на выполненные работы – не менее года.
СВАРОЧНЫЕ РАБОТЫ
БЛОКИ ЦИЛИНДРОВ И ГОЛОВКИ БЛОКОВ
(чугунные и алюминиевые)
Трещины и проломы в ремонтируемых блоках цилиндров и головках блоков устраняют сваркой. Кроме того, восстанавливают поломанные, отломанные и даже утраченные элементы крепления – лапы крепления двигателя, кронштейны, проушины и бобышки. Раковины на плоскости сопряжения блока и головки заваривают. Если нужно, то после сварки восстанавливают резьбы и привалочные плоскости механической обработкой.
Пример.
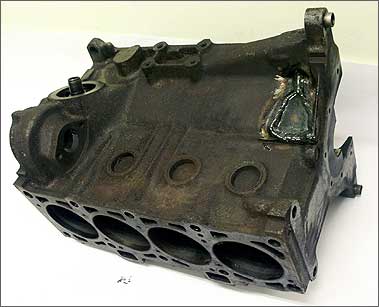
Типичная ситуация: шатун проломил стенку блока, пролом закрыт приваренной
заплаткой. Применительно к блокам это простой ремонт, но такие повреждения встречаются часто.
КАРТЕРЫ И КОРПУСА ДВИГАТЕЛЕЙ, КОРОБОК ПЕРЕДАЧ, СЦЕПЛЕНИЯ, БОРТОВЫХ РЕДУКТОРОВ (алюминиевые, чугунные и стальные)
При ремонте картеров и корпусов устраняют трещины и проломы, восстанавливают отломанные или утраченные проушины и крепежные бобышки с резьбовыми отверстиями. Если при аварии утеряны фрагменты, то изготавливают новые, подгоняют их по месту и приваривают.
Пример 1
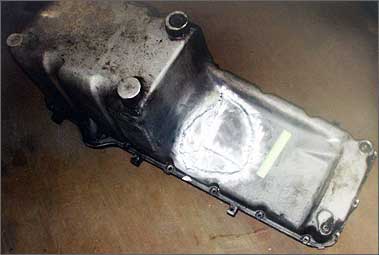
Алюминиевый картер двигателя после ремонта. Такое бывает часто: картер проломлен, выломанная часть разбита на куски, но все они сохранились. При ремонте отломанные части картера состыковали по изломам и зафиксировали их положение сваркой.
Пример 2
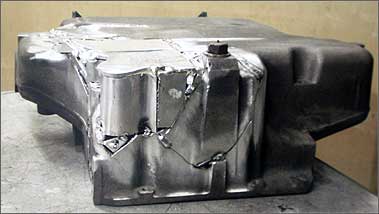
Более сложная, но реже встречающаяся ситуация, чем на предыдущем снимке. У алюминиевого картера при аварии выломан большой кусок, он разбит на фрагменты и часть фрагментов утеряна. При подготовке этого картера к сварке взамен утерянных фрагментов изготовили новые и закрепили их прихватками в нужном положении (один из фрагментов потребовалось не только вырезать, но и фигурно изогнуть).
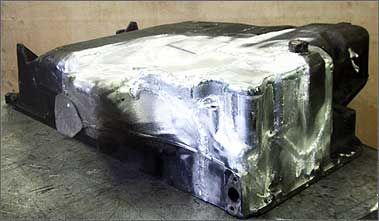
Тот же картер после сварки, подготовленный к испытанию на герметичность керосином (покрыт меловой краской).
ВЫПУСКНЫЕ КОЛЛЕКТОРЫ
Выпускные коллекторы изготавливают, в основном, из чугуна, реже - из жаростойких сталей. На мотоциклах встречаются и алюминиевые водоохлаждаемые коллекторы.
Чаще всего к нам поступают чугунные коллекторы. Сложность их ремонта обусловлена не только тем, что они чугунные (чугун плохо сваривается), а тем, что нередко их материал – так называемый «горелый чугун». Горелым называют чугун, который в процессе эксплуатации многократно сильно нагревали и охлаждали. При этом изменяется структура чугуна, он становится пористым и считается несваривающимся. При традиционных приёмах сварки такой чугун чаще всего трескается сразу, при сварке, реже – через короткое время при эксплуатации. Разработанные нами технологии, как правило, позволяют надежно сваривать и такие коллекторы. Единичные исключения встречаются очень редко.
Трещины в чугунных коллекторах заваривают, развалившийся на куски коллектор сначала собирают, закрепляют в собранном состоянии на жестком основании, затем разделывают стыки под сварку и заваривают их. Нередко после сварки выполняют механическую обработку, обеспечивая совпадение плоскостей тех поверхностей, которыми коллектор прижимают к блоку цилиндров. В стальных коллекторах при ремонте заваривают трещины и дыры. При этом нужно обеспечивать жаростойкость сварных соединений, иначе отремонтированный коллектор долго не прослужит. Затруднения в обеспечении жаростойкости обусловлены тем, что марка стали, из которой изготовлен коллектор, обычно неизвестна, а сварочные свойства разных сталей весьма различны. Наши инженеры надежно решили эту проблемы.
Из жаростойкой стали изготавливают и новые выпускные коллекторы (по индивидуальным заказам). У мотоциклов с алюминиевыми водоохлаждаемыми выпускными коллекторами может нарушаться герметичность ка внутренней, так и наружной стенки рубашки охлаждения. Сложность их ремонтной сварки обусловлена, главным образом, маленьким расстоянием между стенками рубашки - менее трёх мм. Необходимо восстановить герметичность поврежденной стенки, не перекрыв охлаждающей жидкости проход между стенками. Соответствующая технология нами разработана.
Пример 1
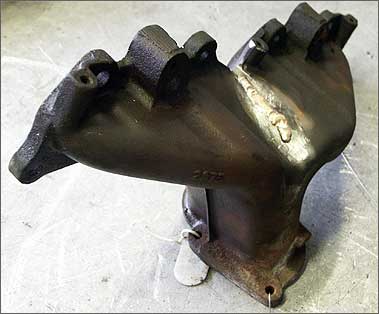
Чугунный коллектор с заваренной трещиной
Пример 2
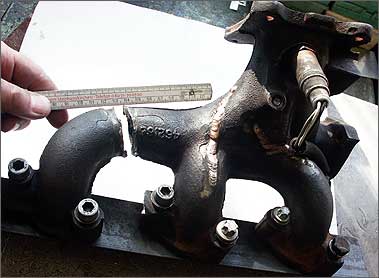
Чугунный коллектор собран из кусков. Один разлом уже заварен, второй – разделан под сварку (подготовлен к сварке).
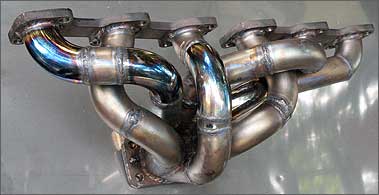
Коллектор из жаростойкой стали, изготовленный нами по индивидуальному заказу.
РЕМОНТ КОВША ЭКСКАВАТОРА
У доставленного в ремонт ковша были изношены рабочая кромка и обоймы крепления зубьев. Верхняя часть большинства обойм была вырвана. Кроме того, были обнаружены трещины на проушинах крепления ковша к экскаватору.
При ремонте:
- срезали автогеном остатки обойм крепления зубьев ковша и подрезали по прямой его переднюю кромку, чтобы не подгонять по форме каждую вставку,
- изготовили и вварили стальные вставки, скомпенсировав износ рабочей кромки ковша,
- изготовили и приварили стальные пластины, сформировав обоймы крепления зубьев ковша,
- наплавили износостойким сплавом наиболее интенсивно изнашивающиеся участки рабочей
кромки ковша и обоймы крепления зубьев,
- заварили трещины на проушинах крепления ковша.
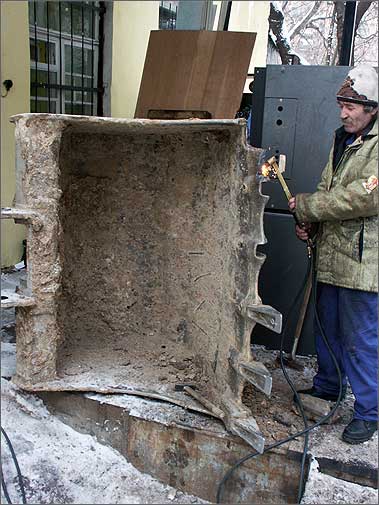
начало ремонта – резка автогеном обойм крепления зубьев и передней кромки;
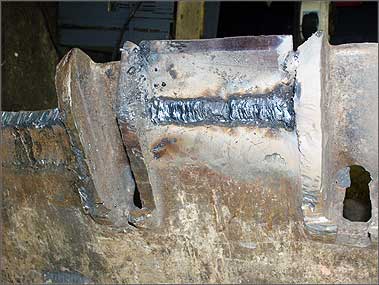
срезана изношенная часть обойм крепления зубьев и к передней кромке приварена вставка;
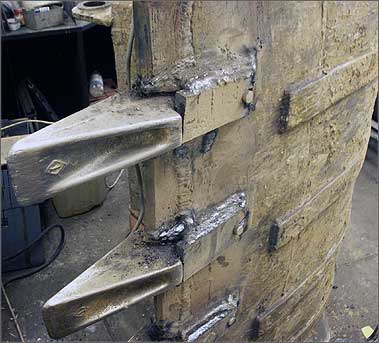
сделаны обоймы крепления зубьев, выточены новые пальцы крепления и зубья вставлены в обоймы;
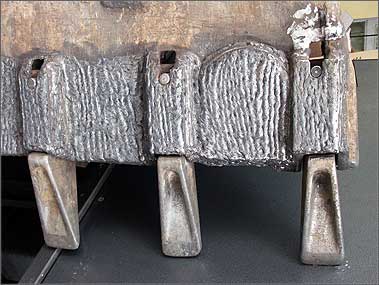
кромку ковша и обоймы зубьев наплавили износостойким сплавом;
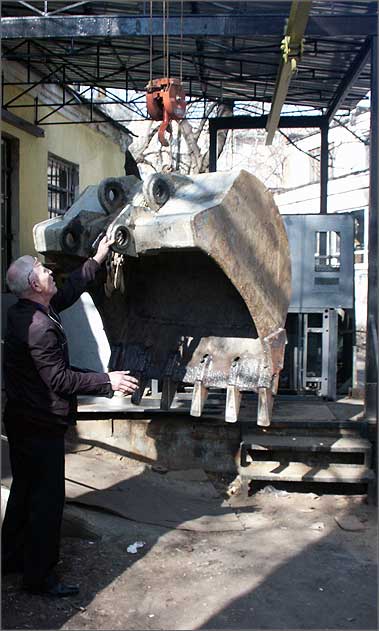
представитель заказчика забирает отремонтированный ковш.
ПОВОРОТНАЯ ТУМБА ЭКСКАВАТОРА
На снимке показана поворотная тумба экскаватора с отломанной проушиной. Это литая деталь из серого чугуна, на которую опирается стрела экскаватора. Длина её – порядка 60 см. Стрелу и тумбу соединяют два стальных пальца, каждый из которых проходит через проушину в тумбе и входит в проушину стрелы.
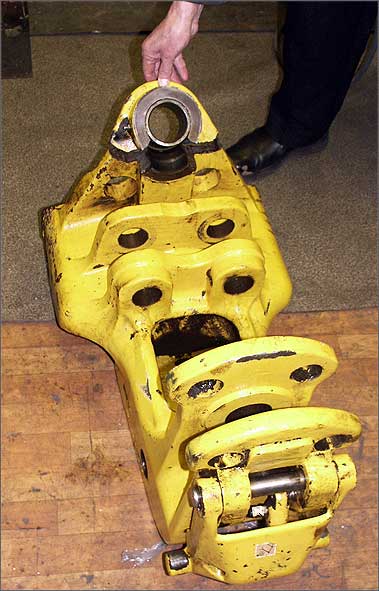
На этом снимке ниже - сломанная проушина с кольцом подшипника показана вблизи. При восстановлении проушины необходимо было преодолеть два препятствия:
1) проушина тумбы – сильно нагруженная деталь, и обеспечить её надежную работу после сварки (деталь чугунная!) по мнению многих специалистов невозможно. Нам говорили, что сваренная проушина обязательно сломается, стрела упадёт и хорошо, если никого не покалечит;
2) отверстия в обеих проушинах должны быть строго сосны. При сварке невозможно обеспечить соосность с требуемой точностью, даже если точно и жестко закрепить детали перед сваркой в специальном стапеле. После снятия со стапеля проушину поведёт за счёт упругих деформаций и соосность будет нарушена.
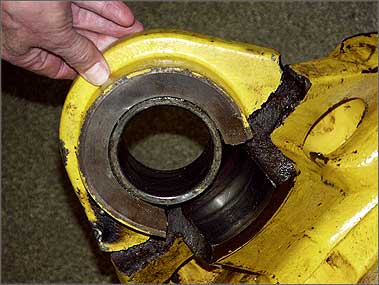
Та же проушина после сварки. Наша технология гарантировала прочность сварного соединения. Однако, приварить отломанную часть проушины так, чтобы деформация была неощутимой, было невозможно. Поэтому технологический процесс ремонта пришлось сделать многоступенчатым, чередуя механическую обработку и сварку.
Соосность отверстий была обеспечена и стрелу экскаватора установили на место без всяких затруднений. Первые дни после ремонта люди разбегались, когда экскаватор начинал работать: ожидали, что чугунная тумба сломается и стрела рухнет на землю. Экскаватор с отремонтированной нами тумбой отработал уже больше года.
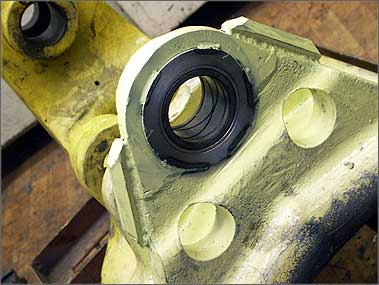
РЕМОНТ ТОПЛИВНЫХ БАКОВ
Чаще всего к нам поступают топливные баки больших грузовиков и мотоциклов, реже – импортных легковых автомобилей и строительной техники, а также топливные и масляные баки разнообразных механизмов (компрессоров, гидроприводов, дизель-генераторов и др.).
Основные причины ремонта:
- трещины,
- пробоины,
- вмятины,
- течи из-за коррозии,
- отрыв внутренних перегородок,
- повреждение заливочной горловины.
Все дефекты и стальных, и алюминиевых баков устраняют сваркой. Для закрепления оторвавшихся перегородок и для выправки больших вмятин бак приходится вскрывать, а потом опять заваривать. По просьбе заказчиков нередко приходится удлинять (реже - укорачивать) баки, заменять или переставлять на новое место горловины и другие элементы.
Баки больших грузовиков для международных перевозок ремонтируют так, чтобы не было видно следов ремонта: иначе пограничники ряда стран (например, Германии) не пропускают машину через границу.
Места сварки после ремонта обязательно проверяют на герметичность. В некоторых случаях проверяют на герметичность весь бак целиком.
Для ремонта бака необходимо снять его с машины, слить остатки топлива и вымыть только снаружи. Заказчик может сделать это сам, а может поручить нам, оставив, если нужно, машину на бесплатной охраняемой стоянке. Пропаривать или промывать бак изнутри не требуется.
Пример ремонта
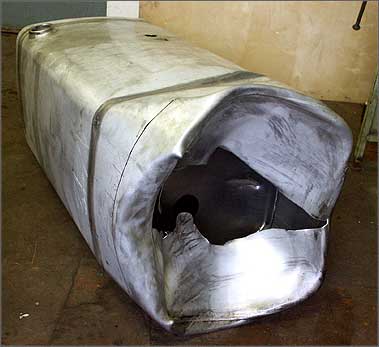
Алюминиевый бак магистрального грузовика после аварии. Линией намечена
плоскость разреза.
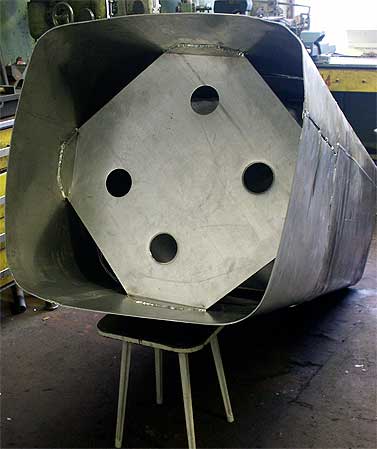
Этот же бак в процессе ремонта: порванное днище вместе с сильно помятой
частью бака отрезали, остальное выправили и, по просьбе заказчика, удлинили бак на 380 мм (сделали и приварили вставку корпуса и дополнительную перегородку внутри).
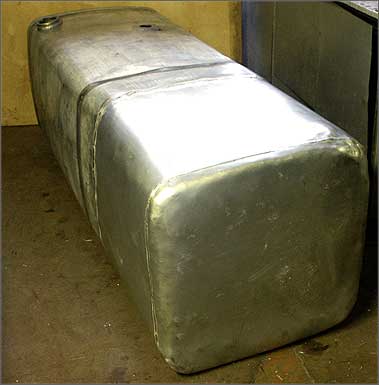
Бак после ремонта (вместо порванного дна отформовали и приварили новое). Длина бака после ремонта – более 2 м.
Ещё пример ремонта.
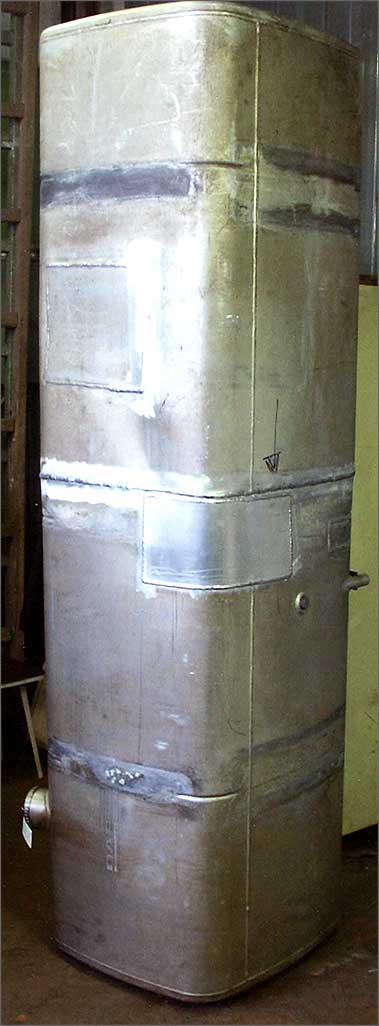
Бак похожей конструкции, но ещё большего размера: его сварили из двух относительно небольших старых баков и заодно приварили заплатки, устранив утечки топлива из-за коррозии.
|